Reactor Temperature Control System丨TCU
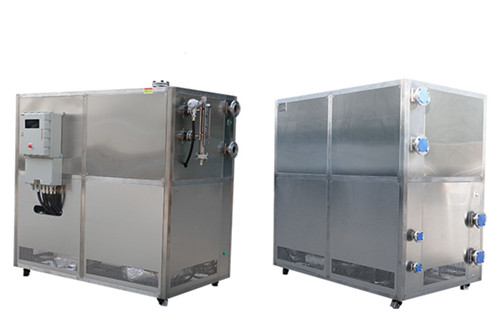
AppliCAtions:
- Single-fluid heat transfer temperature control system, which can achieve temperature control from -120 degrees to 300 degrees;
- The auxiliary heating system can be automatically turned on according to the demand to reduce the pressure of steam usage;
- Control the temperature of the whole reaction process through accurate and fast calculation;
- Optionally control the reaction process temperature and single fluid temperature;
- Standardized interfaces are reserved, and cold and heat source heat exchange modules can be added according to actual needs.
Principle of Temperature Control Unit
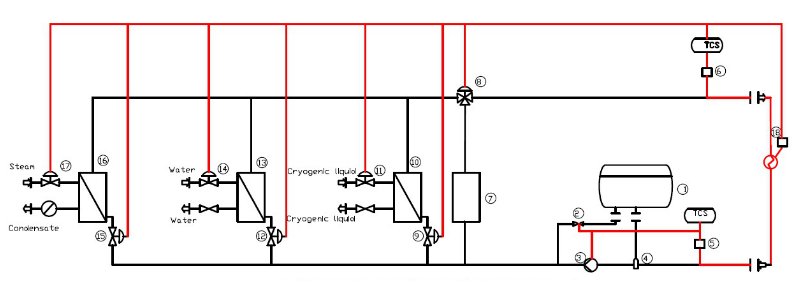
TCU temperature control system can achieve dynamic temperature control from -120°C to 300°C, using the existing infrastructure of thermal energy (such as steam, cooling water and ultra-low temperature liquid – “primary system”) to be integrated into the temperature control system for process equipment. in single-fluid systems or secondary circuits. This completes that only one heat transfer liquid flows into the jacket of the reaction vessel (instead of directly passing steam, cooling water or ultra-low temperature liquid), and the temperature of the entire reaction process is controlled by calculation.
Our TCU temperature control systems are available in ZLF and SR models as well as DCS integrated temperature control systems.
Models | ZLF(N/NS/NH/NSH) | SR(N/NS/NH/NSH) |
Medium Temperature Range | -45~250℃ | -120~250℃ |
Heat Exchanger Area | 3.5㎡~20㎡ | 3.5㎡~20㎡ |
Temperature Control Selection | reaction material | reaction material |
Material Temperature Control Accuracy | ±1℃ | ±1℃ |
Circulating Pump | 150L/min~750L/min 2.5bar | 200L/min~750L/min 2.5bar |
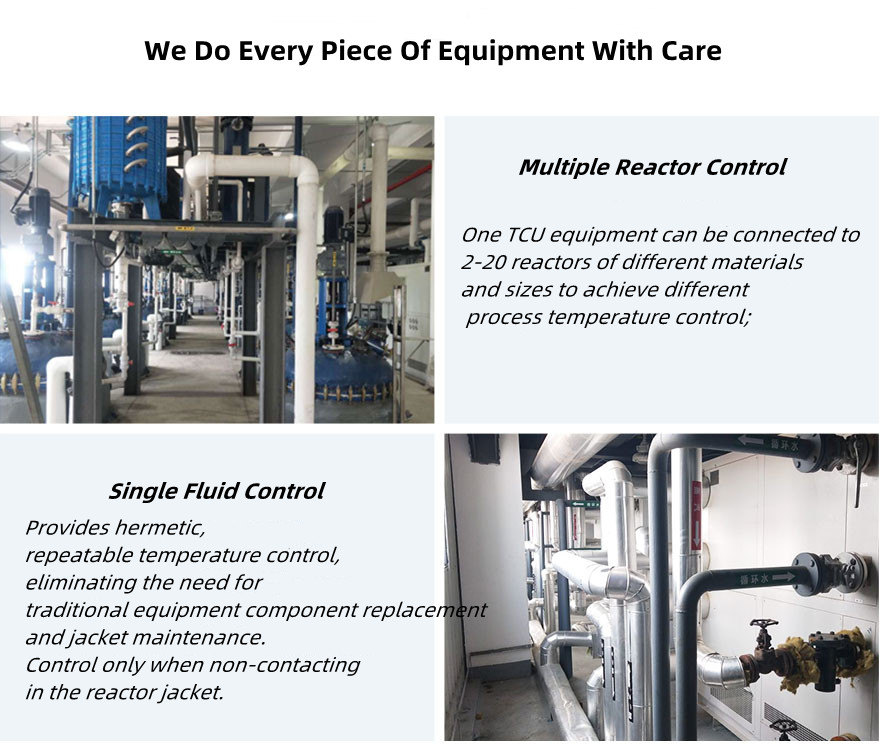
Video Introduction
Temperature process control (control reaction kettle material temperature):
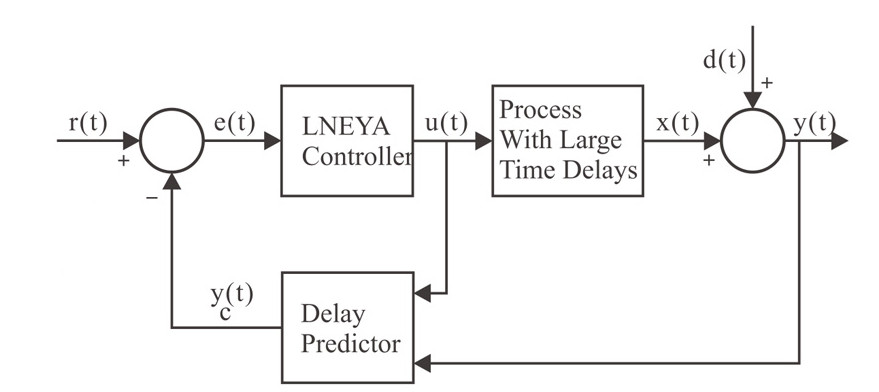
1.The method of changing the control setting value can respond to the system lag in the process as soon as possible, and obtain a small system overshoot. The control consists of two groups of PID (each group of PIDs are variable) control loops, these two groups of control loops are called: the main loop and the slave loop, the control output of the main loop is used as the set value of the slave loop. The system adopts a feedforward PV, and the output of the PID operation result of the main control loop is combined with the feedforward PV signal as the set value of the slave control loop. Through this gradient control of the temperature change, the temperature control accuracy of the system is guaranteed. (General anti-lag cascade control);
2.The specially designed lag predictor (model-free self-building tree algorithm) generates a dynamic signal yc(t) instead of the process variable y(t) as a feedback signal. Generate an e(t) signal to the controller, so that the controller predicts the control action without a large delay, so that the controller can always generate an appropriate control signal. That is to say, even if there is a large lag, this dynamic signal yc(t) can keep the feedback loop working properly. While using general PID to control a process with a significant time lag, the controller output is not suitable for the lag time due to The feedback signal keeps increasing, resulting in a large overshoot of the system response and even out of control of the system.
3.Through three-point sampling (material temperature point, temperature control system outlet temperature, temperature control system inlet temperature), through the combination of our company’s own model-free self-building algorithm and general anti-lag cascade algorithm.
Other Star Products
Water Chillers
Temperature Control Range: -150°C to +50°C
Application: Various Reactors (Microchannels, Glass, Jacketed Reactors, etc.), Distillation or Extraction System etc..
IC Shock Test Chiller
Temperature Control Range: -120°C to +300°C
Application: Temperature shock of chips, modules, integrated circuit boards, electronic components etc..
Vehicle Test Chillers
Temperature Control Range: -40°C to +135°C
Application: Battery life test,Fuel injector, pump test bench,Airbag Test,Component testing of power modules etc..
Cooling and Heating Systems
Temperature Control Range: -120°C to +350°C
Application:High Pressure Reactor/Double-Layer Glass Reactor/Double-Layer Reactor,Microchannel Reactor,Steaming System etc..